Spiral Heat Exchanger
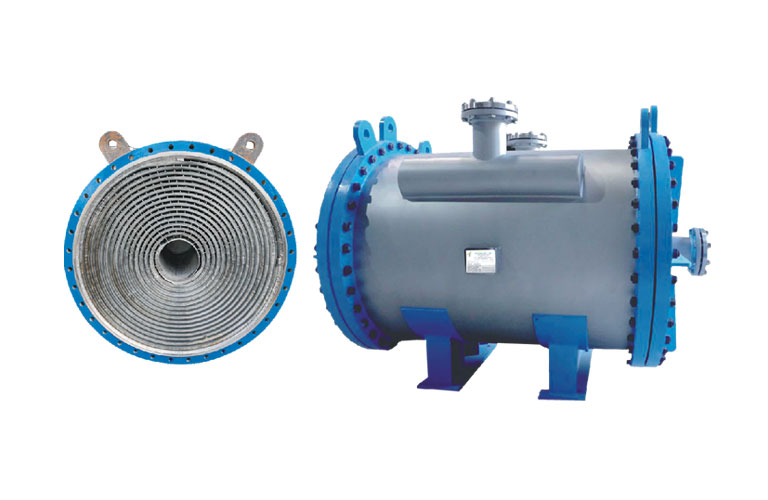
Spiral Heat Exchanger
NOVA TECH Spiral Heat Exchanger is specifically designed to tackle the most challenging heat transfer tasks. Its coiled, spiral-shaped design, with two long metal sheets wound together to create parallel channels, enables efficient heat transfer through counterflow, allowing fluids to flow in opposite directions. This design accounts for flow rates, particle sizes and pressure drops in fouling fluids.
NOVA TECH Spiral Heat Exchangers are the ultimate problem solver for liquid-to-liquid and two-phase duties, even in cases of frequent fouling from dirty media or limitations in pressure drop and floor space. With robust, efficient, and compact designs, installation and maintenance costs remain extremely low.
Proper maintenance is crucial to ensure their optimal performance and longevity by Cleaning, Inspection, Maintenance, Fluid Analysis, Maintenance of Support Systems, Training and operator awareness. The applications of heat exchangers are diverse and found in various industries i.e., Power Plant, Wastewater treatment, Pharmaceuticals, Chemical Processing, Refineries, HVAC systems, Food and Beverages Industries and Refrigeration.
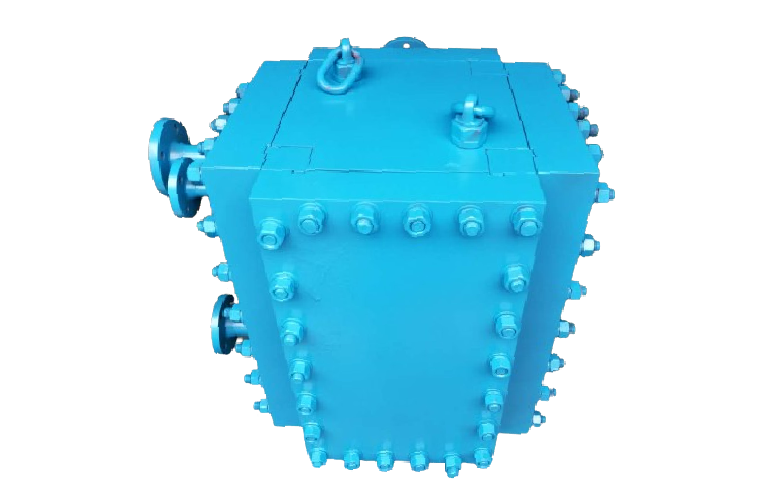
Compabloc Heat Exchanger
NOVA TECH Compabloc Heat Exchanger efficiently transfers heat between two fluids using a series of corrugated metal plates. The plates, typically made of stainless steel or corrosion-resistant materials, create turbulence for enhanced heat transfer. With a compact design and counter-flow arrangement, they offer high heat transfer efficiency and are suitable for space-limited installations. Easy to clean and maintain, the welded plate design reduces the risk of leaks and ensures resistance to temperature and pressure variations.
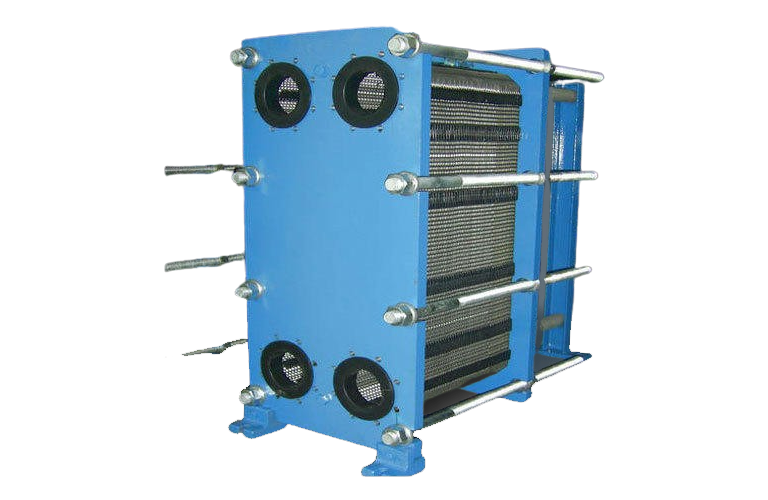
Plated Heat Exchanger
NOVA TECH Plated Heat Exchanger efficiently transfers heat between two fluids using stacked metal plates with ridges and grooves. It maximizes heat transfer surface area and promotes turbulent flow for improved efficiency. Advantages include high heat transfer efficiency, compact size, flexibility, cost-effectiveness, and easy maintenance.
Plated heat exchangers find applications in various industries, commonly used for heat recovery and heat exchange between fluids of different temperatures, as well as cooling or heating processes.
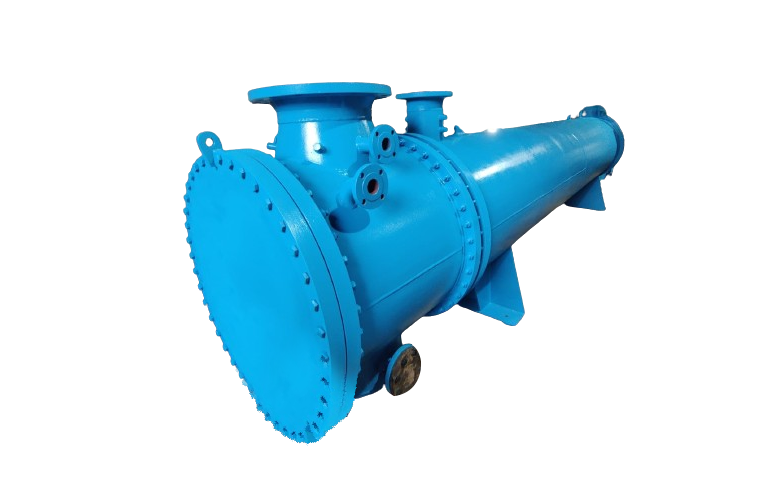
Shell and Tube Heat Exchanger
NOVA TECH Shell and Tube Heat Exchanger is a versatile heat transfer device to exchange heat between two separate fluids. It consists of a cylindrical shell enclosing a bundle of tubes, allowing efficient heat transfer. Key components to be considers are shell, tubes, tube sheets, baffles, and fluid flow arrangements.
Heat is transferred through tube walls from the hot fluid to the cold fluid due to the temperature difference. Shell and tube heat exchangers known for their high efficiency, robust construction, and ability to handle high-pressure and high-temperature conditions. It’s used in almost every type of industries.
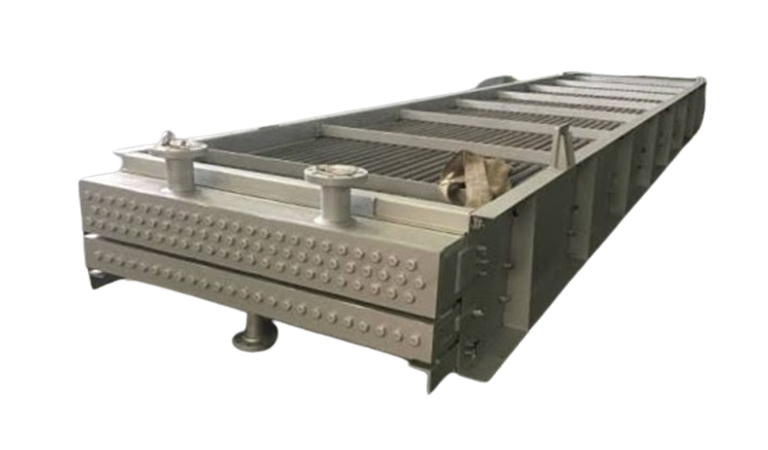
Fin Fan Cooler
NOVA TECH Fin Fan Cooler cools fluids by exchanging heat with ambient air. It consists of finned tubes arranged in a fan-like configuration to maximize surface area for heat transfer. Operating on convective heat transfer, hot fluid flows through the tubes and ambient air is blown over the fins, cooling the fluid. Fin fan coolers are self-contained, cost-effective. Proper design, fan sizing and maintenance are crucial for optimal cooling performance.
Few applications include cooling of hydrocarbon gases in oil and gas processing plants, cooling of steam condensate in power plants, cooling of process fluids in chemical plants and cooling of air in HVAC systems. They are particularly beneficial in situations where a water supply or water cooling is limited or not available.
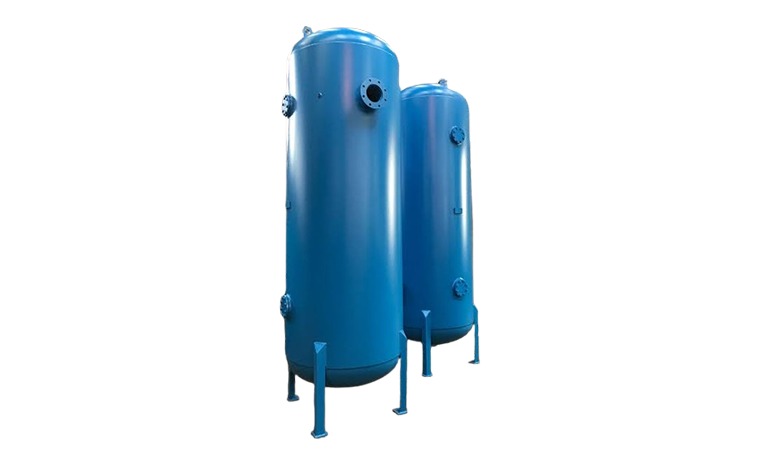
Spiral Condenser
NOVA TECH Condenser transforms hot vapor or gas into a liquid state by transferring heat to a cooling medium. It finds applications in refrigeration, air conditioning, power plants, and chemical processing. The cooling medium can be water, air, refrigerant or other suitable substances.
Our Condensers efficiently remove heat from vapor or gas streams and play a crucial role in industrial processes and systems. Our design team consider the factors such as the desired cooling capacity, operating pressure and temperature, condensing medium flow rate, material selection and fouling considerations need to be taken into account to ensure optimal performance and efficiency.